Jeff Bezos’ Blue Origin has teamed up with Auburn University’s National Center for Additive Manufacturing Excellence (NCAME)—a global leader in material science and additive manufacturing (AM) research—to tackle critical challenges in 3D printing copper, a metal vital for next-generation aerospace systems. This collaboration highlights Auburn University’s pivotal role in advancing AM technologies, with Blue Origin donating two advanced EOS M290 3D printers to accelerate breakthroughs in copper-based additive manufacturing.
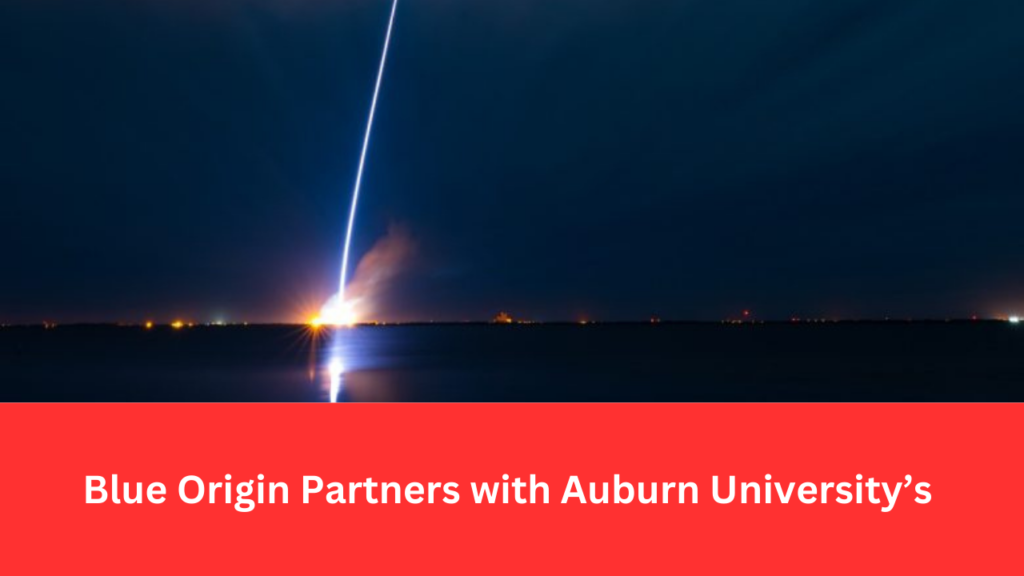
Auburn University’s NCAME Leads Copper 3D Printing Breakthroughs
Copper’s exceptional thermal conductivity makes it ideal for rocket engines and heat exchangers, but its high reflectivity and thermal properties pose unique challenges for laser-based 3D printing. Traditional systems struggle to melt copper powder efficiently, as most laser energy is reflected, leading to uneven melting and potential defects.
“The EOS M290 systems donated by Blue Origin enable us to overcome these barriers,” said Dr. Nima Shamsaei, NCAME Director and Philpott-WestPoint Stevens Distinguished Professor at Auburn University. “These printers are uniquely suited to handle copper’s complexities, particularly with alloys like GRCop-42, which can be printed using standard infrared lasers.”
Why Copper 3D Printing Matters for Aerospace
Copper’s role in spaceflight cannot be overstated. It is critical for:
- Rocket engine components requiring extreme heat resistance.
- Thermal management systems in reusable launch vehicles like Blue Origin’s New Glenn.
- Lightweight, high-performance parts for crewed missions, including the upcoming all-female New Shepard NS-11 flight featuring astronaut Katy Perry.
However, copper’s high thermal conductivity disperses laser heat rapidly, creating inconsistent melt pools. Auburn’s NCAME leverages its expertise in material characterization and modeling to optimize printing parameters, ensuring structural integrity for Blue Origin’s missions.
Auburn University’s Cutting-Edge Research Infrastructure
The two new EOS M290 printers expand NCAME’s existing capabilities, allowing researchers to fast-track applied studies tailored to Blue Origin’s needs.
“With these systems, we’re accelerating research into copper alloys that meet aerospace demands,” emphasized Shamsaei. Auburn’s NCAME has pioneered AM innovations since 2017, supported by partnerships with NASA, the U.S. Army, and now Blue Origin.

Blue Origin’s Vision and Auburn’s Role in Advancing AM
Blue Origin recently marked milestones like the New Glenn rocket’s debut launch and the NS-11 crewed mission, underscoring its commitment to reusable spaceflight. Auburn’s research directly supports these efforts by enabling reliable, large-scale 3D printing of copper components.
“Blue Origin is at the forefront of space exploration,” said Shamsaei. “This partnership exemplifies how academia and industry can collaborate to solve tomorrow’s challenges today.”
The Future of Additive Manufacturing in Aerospace
The collaboration between Auburn University and Blue Origin signals a transformative shift in AM adoption for aerospace. Key focus areas include:
- Process Optimization: Refining laser settings for copper alloys.
- Defect Reduction: Ensuring printed parts meet rigorous safety standards.
- Scalability: Developing methods for mass-producing AM components.
By combining Auburn’s academic excellence with Blue Origin’s engineering prowess, this partnership promises to redefine manufacturing for space exploration.